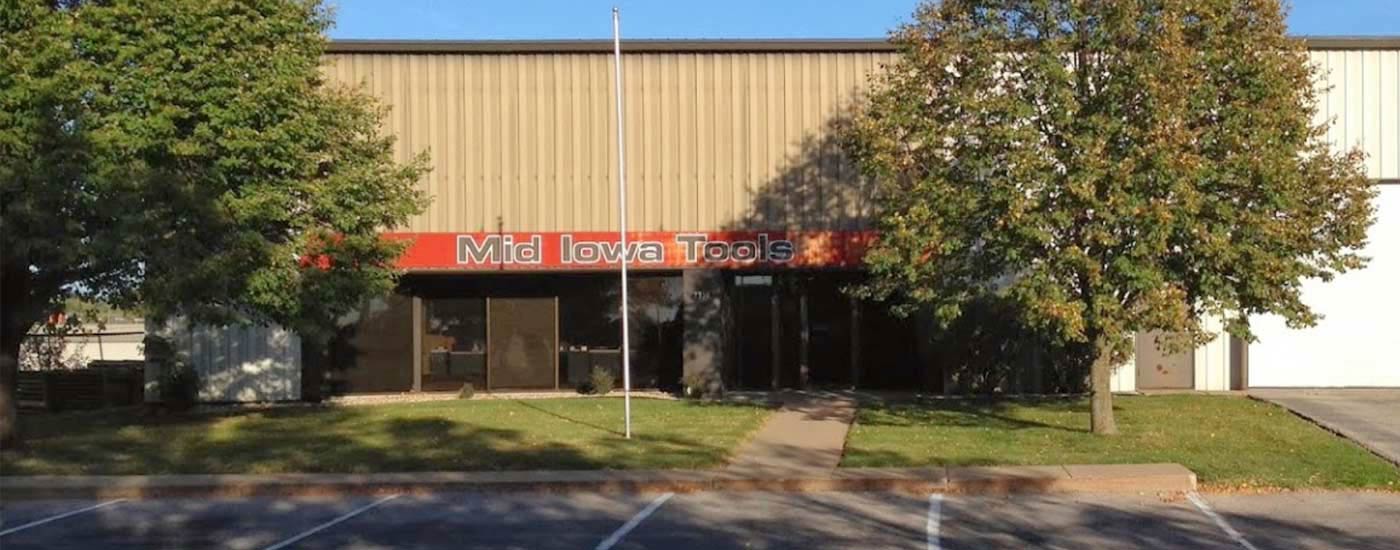
Air Audits
Our Services Compressed Air Audits
Understanding Compressed Air Audits
What Can They Do for You?
Manufacturing facilities spend around 40% of their total energy costs on compressed air alone, making an efficient compressed air system critical for maintaining a healthy bottom line. Unfortunately, not all systems operate in the most efficient manner possible, and we see it every day – compressors not appropriately sized, outdated technology, air leaks, pressure drops – the list can go on and on.
Increasing energy costs is a widespread concern. The U.S. Department of Energy has estimated that over 50% of industrial air compressors are not running efficiently, resulting in 3.2 billion dollars of energy waste annually. The good news is that manufacturers that dedicated resources to lowering energy costs were able to save upwards of 15% annually with a payback of fewer than two years.
So, how can you ensure an efficient compressed air system at your plant?
Uncover the Health of Your System
Performing a compressed air audit of your system is the first step in determining issues that could be hindering your unit’s efficiency and unnecessarily increasing energy costs. There are several levels of compressed air audits that can be performed – walk-through assessment, system assessment, or a full system audit.
Walk-through Evaluation
This process typically takes ½ to 2 days and includes an overview of the plants compressed air system including an analysis of the distribution system to check for leaks, pressure drops, and compressor sizing issues. The compressed air system will be mapped out, and a report of findings and solutions will be proposed.
System Assessment
For a more thorough review, a system assessment is available that includes a walk-through as well as readings collected to identify system dynamics. The compressed air system mapping will feature pressure and demand profiles. The findings of the report and the proposed solutions will be provided at the conclusion of the assessment.
Full System Audit
The system audit is the most comprehensive review and takes around 3 to 10 days with little to no impact on current running procedures. Full compressed air system audits include:
- Energy usage data logging – logs the energy the air compressors are consuming.
- Air measurement – identifies a factory’s true compressed air demand and operating schedule.
- Air leak detection & control – identify how much air is being lost due to leaks.
- Air quality – measures the number of particulates in the air system such as water and oil.
- Maintenance review – assesses the effectiveness of the current maintenance plan
- Monitoring & control program – makes recommendations to maintain optimum efficiency.
Manufacturing Benefits of an Air Audit
Manufacturers using compressed air regardless of the industry – food and beverage, automotive, textile, power, electronics, plastics to name a few will often find that a compressed air audit will pay for itself. Depending on the results of the audit, manufacturers can expect to see improvements in energy efficiency and system reliability and lower operating costs.
As an example, during an audit, some manufacturers find that their plant air systems operate at a higher pressure than the actual demand of the plant due to pressure drops, air leaks or excessive bends in piping design. If a plant requires 100 psi, but due to air loss they must produce 120 psi, they are wasting 20 psi. Performing an audit of your system can help you identify sources of energy waste like this.
Do Your Homework
Before scheduling an air audit, we welcome you to contact us for a review of your current state to better understand how the type of compressor technology you are employing may be contributing to your energy costs. After this initial review, you may elect to receive a more thorough cost analysis of your current compressed air solution.
Get Started Today!
We can customize our solutions to meet your specific project needs. Give us a call or contact us using our contact form. We can't wait to hear from you!